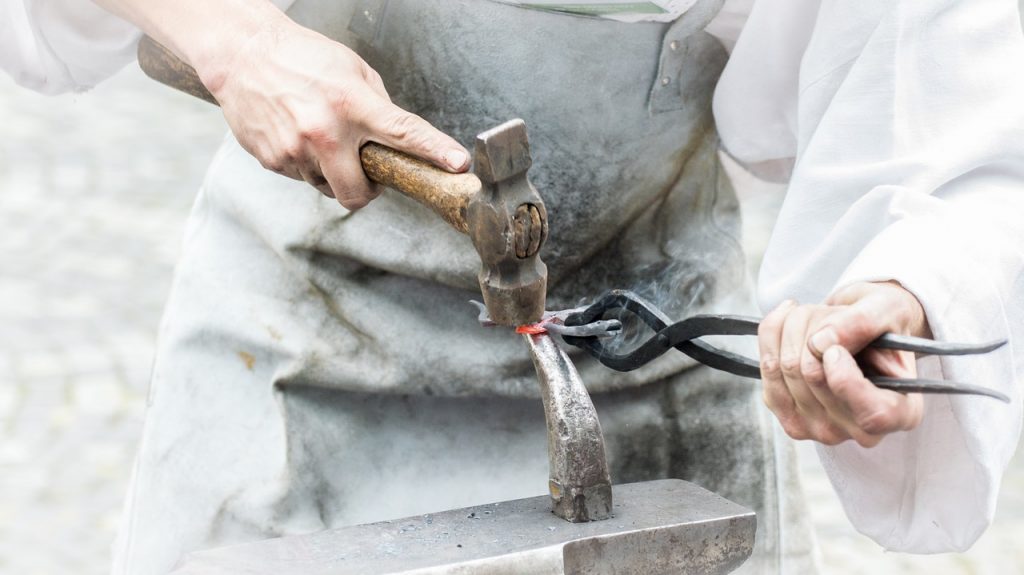
HARDNESS OF STEEL ACCORDING TO THE ROCKWELL SCALE (HRC) Part 2
In Part 2, we will continue discussing the Rockwell scale and take a look at different types of hardness levels.
HARDNESS SCALES
Depth of Penetration (HRc – cone and HRb – ball)
Indenters measure the depth of penetration by loading a certain force. Two types of objects can be used – a cone (HRc), or a ball (HRb). This is a quick and simple measurement and is suitable for cutlery steel.
Vickers Hardness Test (HV)
The Vickers Hardness Test can be used for all types of metals . It uses a diamond indenter with a 136° angle and produces an indentation on the surface of the material being tested on.
Mohs Scale of Minerals Hardness
The Mohs Scale measures the hardness of both minerals and synthetic materials. With this scale, a mineral’s hardness is measured by scratching the mineral against another object of known hardness. The Mohs scale ranges from 1 to 15, with talc having a hardness of 1, and diamond having a hardness of 15.
How Is Hardness Measured According to HRC
A special device is used to measure hardness according to the HRC method. The device comprises of 3 main parts – a diamond cone, anvil, and measuring dial. First, a sample is placed on the anvil and a minor load is applied. With the measuring dial set to zero, a major load is then applied. The depth of penetration from zero-level is measured from the dial.
HRc (cone)
HRc cones feature 120° angles and is impressed on surfaces by applying a force of 100 N. This is the starting point for all measurements, and additional forces of 1400 N to 1500 N is applied and left to ‘dwell’ until sufficient time is passed for indentation to come to a halt. Once indentation comes to a halt, the load is released and the penetration of the depth of the cone is measured in millimeters at the initial load of 100 N. The HRc hardness scale ranges from 100-500h, where h equals penetration depth in mm.
The Properties of Cutting Tools According to HRC Scale
52-54 HRC
52-54 HRC steel is very soft, but solid and inexpensive knives can be made from it. The sharpness is average, not overly smooth or fine. One benefit of these steels is that they’re able to withstand deformation when under large tensile loads due to its high ductility, as knives with lower HRC values bend rather than break when too much force is applied. The structure of these steels means sharpening with whetstones isn’t an easy task. 52-54 HRC steels are great for outdoor knives.
54-56 HRC
54-56 HRC steel is hard enough to be used for kitchen knives but they need to be regularly honed with a honing rod to maintain suitable sharpness. The steel is easy to harden, and most French kitchen knives use 54-56 HRC steel.
56-58 HRC
This level of hardness is common on professional German kitchen knives. Is honed regularly with a steel honing rod, these knives will maintain excellent sharpness, and they’re also easy to sharpen.
58-60 HRC
Quality pocketknives feature 58-60 HRC steel. These knives maintain sharpness for longer periods of time, and they’re easy to sharpen. Brands such as Spyderco, Cold Steel, Buck, and Global are known to use this type of steel.
60-64 HRC
High-quality Japanese knives employ steels with hardness levels of 60-64 HRC. These knives remain sharp for long periods of time; however, they require careful maintenance and they must be used on suitable surfaces in order to prevent breakage or damage to the blade. These knives are brittle and thin, so they’re suitable for only very specific cutting tasks. These knives are easy to sharpen.
65-68 HRC
Powdered steels such as ZDP-189, HAP-40, R2, and Super X fall into this category. Technological advancements in recent years resulted in new types of steels being created that reached hardness levels as high as 64-68 HRC. They’re harder to re-sharpen, however kitchen knives in this category represent the pinnacle of kitchen tools.